PIR & PUR
Polyisocyanurate also referred to as PIR, polyiso, or ISO, is a thermoset plastic typically produced as foam and used as rigid thermal insulation. Its chemistry is similar to polyurethane (PUR) except that the proportion of methylene diphenyldisocyanate (MDI) is higher and a polyester-derived polyol is used in the reaction instead of a polyether polyol. Catalysts and additives used in PIR formulations also differ from those used in PUR. (Pir Polyisocyanurate Boards Pir Insulation Thermal, 2012)
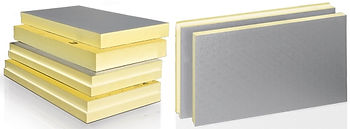

PIR is typically produced as foam and used as rigid thermal insulation. Its thermal conductivity has a typical value of 0.023 W/(m·K) depending on the perimeter: area ratio. PIR foam panels laminated with pure embossed aluminum foil are used for fabrication of pre-insulated duct that is used for heating, ventilation and air conditioning systems. Prefabricated PIR sandwich panels are manufactured with corrosion-protected, corrugated steel facings bonded to a core of PIR foam and used extensively as roofing insulation and vertical walls (e.g. for warehousing, factories, office buildings etc.). Other typical uses for PIR foams include industrial and commercial pipe insulation, and carving/machining media (competing with expanded polystyrene and rigid polyurethane foams).
Effectiveness of the insulation of a building envelope can be compromised by gaps resulting from shrinkage of individual panels. Manufacturing criteria require that shrinkage be limited to less than 1% (previously 2%). Even when shrinkage is limited to substantially less than this limit, the resulting gaps around the perimeter of each panel can reduce insulation effectiveness, especially if the panels are assumed to provide a vapor/infiltration barrier. Multiple layers with staggered joints, ship lapped or tongue and groove joints greatly reduce these problems. (Pir Polyisocyanurate Boards Pir Insulation Thermal, 2012)

Rigid PIR differs from PUR in that it is produced using an excess of the MDI component. In the presence of an appropriate catalyst the excess MDI reacts with itself to form isocyanurate which is characterized by greater heat stability. The resultant PIR insulation products exhibit increased fire performance and reduced combustibility and higher working temperature limits compared to PUR and when incorporated into building products, can meet some of the most demanding fire performance requirements such as those currently stipulated for some applications by the insurance industry.
For develop Architecture

